散劑包裝機作為制藥、食品和化工等行業的重要設備,其設計與生產質量直接關系到產品的包裝效率和質量。隨著工業自動化水平的不斷提高,對散劑包裝機的精度、速度和可靠性要求也越來越高。
一、設計階段的關鍵環節
它的設計始于深入的市場需求分析。設計團隊需要充分調研目標行業的具體需求,了解不同散劑物料的特性、包裝規格要求以及生產環境條件。這一階段還需要分析競爭對手產品的優缺點,確定產品的市場定位和差異化競爭優勢。通過市場調研,可以明確設備需要達到的產能、精度等級和特殊功能要求。
在確定技術參數時,工程師需要綜合考慮包裝速度、計量精度、物料適應性等關鍵指標。包裝速度通常以包/分鐘為單位,需要與生產線其他設備匹配;計量精度則根據物料價值和行業標準確定,制藥行業通常要求更高。此外,還需確定設備的最大最小包裝規格范圍、電源要求、氣源壓力等技術細節,這些參數將直接影響后續的結構設計。
結構設計是包裝機設計的核心環節,包括傳動系統、計量裝置、成型機構和控制系統等主要部件的布局設計。傳動系統需要保證運行的平穩性和精確性;計量裝置根據物料特性可選擇螺桿式、量杯式或電子秤式;成型機構則需適應不同包裝材料的要求。設計過程中需運用CAD軟件進行三維建模和運動仿真,確保各部件協調工作且便于維護。
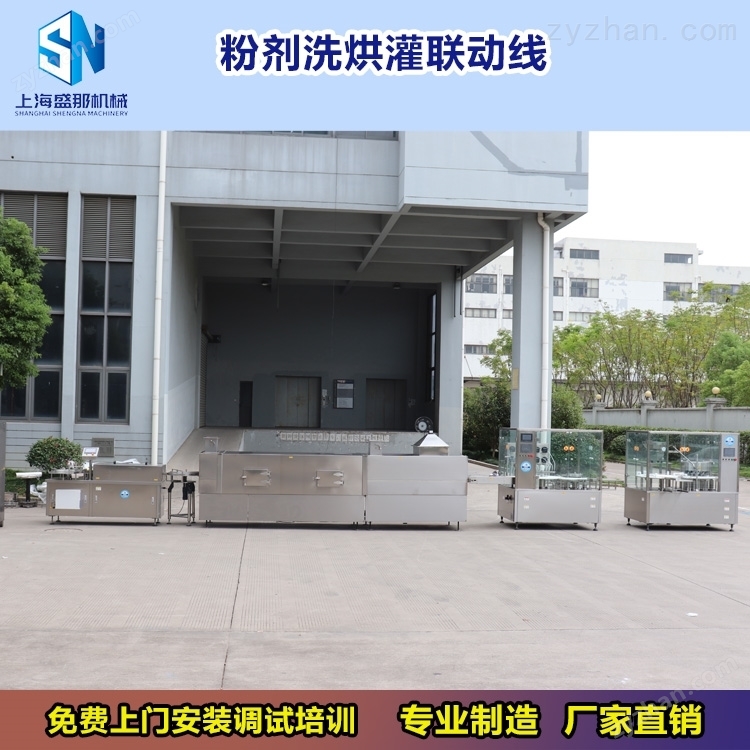
二、生產階段的核心步驟
原材料采購是生產階段的首要步驟,需要根據設計規格選擇適當的金屬材料、電氣元件和標準件。機架通常采用不銹鋼或碳鋼,傳動部件需要耐磨合金鋼,與物料接觸部分則需食品級或醫藥級不銹鋼。采購過程中需嚴格控制材料質量,確保符合設計要求和相關行業標準。
加工制造階段包括機械加工、鈑金成型、熱處理等工藝過程。精密部件如傳動齒輪、計量螺桿等需要數控機床加工以保證精度;大型結構件可采用激光切割或折彎成型。加工過程中需進行工序檢驗,確保關鍵尺寸和形位公差符合圖紙要求。表面處理如拋光、噴涂或電鍍也在此階段完成,以提高設備的耐用性和美觀度。
裝配調試是將各部件組裝成完整設備并驗證其性能的關鍵環節。裝配需按照既定的工藝路線進行,從機架安裝開始,逐步裝配傳動系統、計量裝置和電氣控制系統。調試階段需檢查各運動部件的協調性,調整計量精度,測試不同物料的包裝效果。通過連續空載和負載運行測試,確保設備達到設計性能指標后才能交付客戶。
三、質量控制與性能測試
質量控制貫穿散劑包裝機生產的全過程。來料檢驗確保原材料和零部件質量;過程檢驗監控各生產工序的質量狀況;最終檢驗則對成品設備進行全面測試。關鍵質量控制點包括尺寸精度、表面質量、裝配間隙、電氣安全等。通過建立完善的質量追溯系統,可以快速定位和處理質量問題。
性能測試是驗證設備是否符合設計要求的重要手段。基本測試包括包裝速度測試、計量精度測試、連續運行穩定性測試等;特殊測試可能包括不同物料的適應性測試、溫濕度環境測試等。測試過程中需記錄詳細數據,分析可能存在的缺陷并加以改進。只有通過全部性能測試的設備才能獲得出廠合格證。
市場反饋是產品持續優化的重要依據。通過收集客戶使用過程中的意見和建議,分析設備在實際生產環境中的表現,可以發現設計階段未能預見的問題。定期回訪客戶、建立故障統計數據庫、跟蹤行業技術發展,都是獲取市場反饋的有效途徑。基于這些反饋,企業可以制定產品改進計劃,提升下一代產品的競爭力。